August 25, 2021 by Giovanni Di Maria
Our planet is in danger both from an environmental and a climatic point of view. The production of clean energy, especially energy based on green hydrogen, is driving many companies and industries toward investments on hydrogen-related research aimed at protecting the climate and natural resources. The reduction of greenhouse gases will be much stricter than before, and it is hoped that by 2050, emissions will be eliminated.
Extracting hydrogen from water
Hydrogen is the first element of the periodic table. It cannot be created from scratch, but it can be obtained from water. There are different methods for extracting hydrogen. Some create more pollution than others. Often, hydrogen is produced and consumed in the same manufacturing process, without the need to be separated. With electrolysis, hydrogen can be extracted from water by decomposition. This process allows us to obtain:
One of the simplest methods is to apply an electric current to an aqueous solution. During the process, hydrogen accumulates on one of the electrodes. Collecting and storing the chemical element, and waste disposal, are the most complicated phases in the process.
Hydrogen is the future of the planet
The world is facing one of the most important challenges: achieving zero greenhouse gas emissions in three decades. One of the most promising technologies to address these challenges is green hydrogen. It would make clean mobility possible and could help reduce CO2 emissions in many ways, provided that production, storage, transport, and use are best guaranteed. Infineon’s power semiconductors promise efficient solutions for the production and consumption of green hydrogen and provide the right potential for the future energy system. Using clean energy obviously depends on the scientific progress achieved but even more on the political decisions from governments. The projected percentage of greenhouse gas reductions increases year after year, suggesting that if drastic decisions are not taken, a tipping point could easily be reached. Therefore, emerging applications foresee hydrogen as the main source of energy. Semiconductor manufacturing must obviously follow this development channel, for example, for clean IoT systems. Different types of hydrogen would be available:
- Gray hydrogen, produced from fossil resources, involves the emission of CO2, and of course, this possibility must absolutely be avoided.
- Blue hydrogen is produced from fossil resources with nuclear carbon capture and sequestration technologies.
- Green hydrogen is produced exclusively from renewable energy sources such as hydroelectric, solar, and wind power.
The application areas of hydrogen are many and range from energy storage to fuel storage. Due to its clean nature, it can also replace fossil fuel in many areas. The production of hydrogen alone is obviously not enough. The rise of renewable energies requires adequate large-scale energy storage. Hydrogen production costs are also expected to be extremely low, in the order of $1/kg, at least initially. Hydrogen will be the key to reducing emissions in any sector. Its usefulness in the production and distribution chain will include an efficient system involving:
- Generation and production with clean and non-polluting techniques, carried out with AC and DC electrolysis processes.
- Efficient transmission, thanks to medium- and long-term energy storage.
- Consumption, at significantly lower costs.
Moreover, thanks to the production of new semiconductor power devices, powers ranging from 1 kW to 50 MW and more can be managed without problems. Green hydrogen can have very important uses, on a large scale, in transport, in industrial production, or in high-temperature heating. The production of green hydrogen (see block diagram in Figure 1) requires structures that are necessary for the electrolysis process. Alternating currents will need to be converted into direct currents. Compression structures, auxiliary systems, and controls will follow, obviously managed by electronic communication and safety support systems.
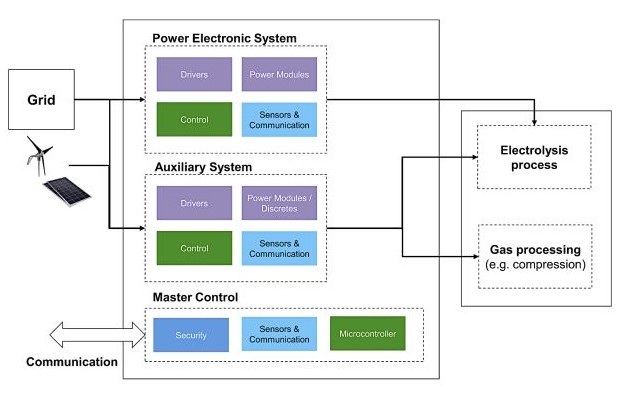
Figure 1: Hydrogen production block diagram (Source: Infineon)
Thyristors for hydrogen electrolysis
Nowadays, systems aimed at straightening high currents are at the forefront. Thyristors and IGBTs can manage enormous amounts of energy, but what is most interestingly sought is to maximize the power density by trying to lower conduction losses. Cooling systems are also a crucial point for thyristors, which can also be protected by fuses that are usually present in the system. AC-coupled thyristors for green hydrogen production (see Figure 2) have many advantages:
- The circuit is less complex.
- The final system is cheaper than the one with an IGBT.
- They are more robust than IGBTs.
- As mentioned before, it is possible to implement protection with fuses.
- They switch off automatically when the voltage crosses zero.
- Maximum power density is obtained with low conduction losses.
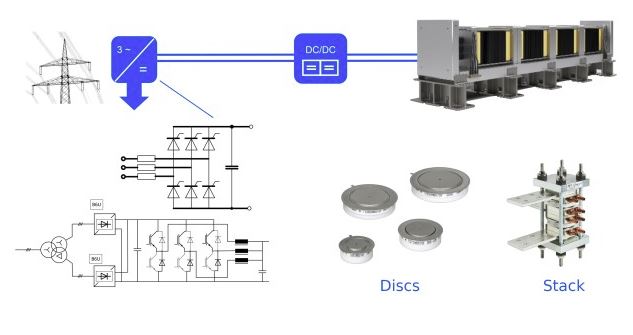
Figure 2: The circuit is less complex with thyristors (Source: Infineon)
In the principal diagram, at the top left, you can see the high current rectifier, and at the top right, you can see the electrolyzer, which produces hydrogen. The circuits used are the typical thyristor rectifier for high-current applications (currently up to 20 MW and above) and the diode rectifier with the IGBT DC/DC converter. With thyristors, there may be some harmonics on the DC line that are caused by the electrolyzer. They do not affect the output power of the electrolyzer and are represented by discs from 111 mm to 150 mm or can be combined in a single stack. The latter contains the connections, the thyristors, and the cooling discs and constitutes a ready-to-assemble system. With IGBTs, harmonics are reduced but have higher losses. Depending on the final needs, one of the two systems can be chosen to appropriately regulate the amount of current that will pass through the electrolyzer. With thyristors, this adjustment can be done more easily.
Different models for a lot of power
Infineon’s Power Block modules are available in different varieties (as shown in Figure 3), depending on the required power class. The smallest models are 50 mm and 60 mm and can be used with diode or thyristor rectifiers. The 150-mm disc device is instead usable for a few-megawatts–higher power. The most common models are 111-mm, 100-mm, and 75-mm models. As for the normal stacks, they are equipped with liquid cooling so that full power can be delivered. Some models can also work up to 3.6 kV.
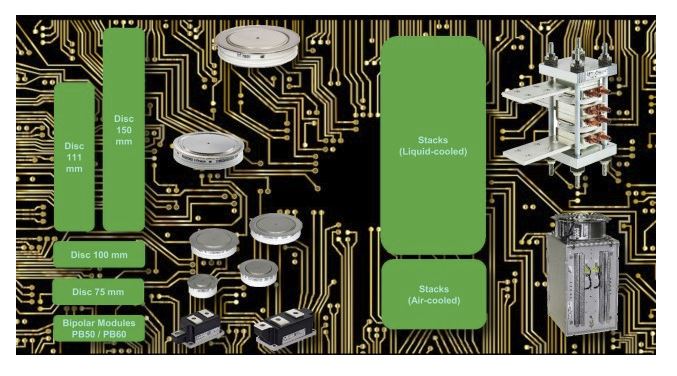
Figure 3: Different rectifier solutions (Source: Infineon)
Let’s now examine a hydrogen fuel-cell electric vehicle. It consists of the battery system and the fuel cells. To better understand how the system works, imagine that the batteries are exhausted or that the user is drawing energy from the grid using the cable with an AC or DC charging circuit. When the battery is full, the cable is disconnected and the battery can power the inverter, which, in turn, powers the motor. There are several possibilities with a fuel cell:
- A very small battery (1–2 kWh) can be used and a charging system is not necessary. The battery is mostly used as a buffer and the main energy comes from the fuel cell, which will power the inverter.
- Larger batteries (10–20 kWh) can be used, which allow a range of more than 5,000 km. In this case, a charging system is required.
The most important unit is represented by the fuel-cell system (see Figure 4), inside which the hydrogen passes. The air that passes from the system is compressed and sent to a fuel cell. Then the electrical voltage is applied. The converters must be designed to be highly efficient. After the reaction, the gases must be discharged and sent into the atmosphere. Thermal management that controls the fuel-cell temperature is important at this stage. The whole system consists of five subsystems:
- The AF subsystem
- The hydrogen subsystem
- The subsystem of the proton exchange membrane
- The exhaust subsystem
- The thermal management subsystem
In the first subsystem, the presence of a filter is essential to eliminate odors from the air that could poison the proton exchange membrane. In this phase, pressure, temperature, and air flow must be continuously measured. Also, as compression raises the temperature, a cooler and humidifier are required to get the right temperature and humidity level for the proton exchange membrane.
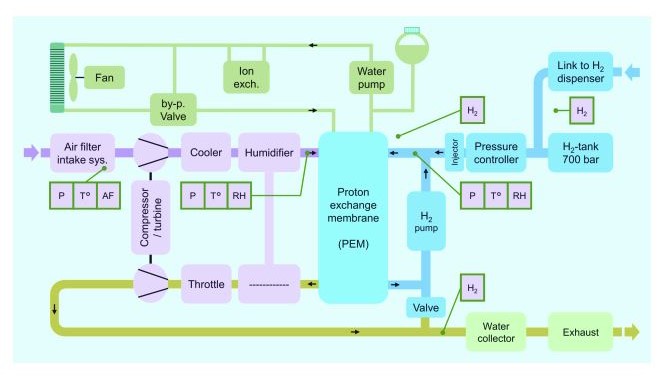
Figure 4: The block diagram of the operation of a fuel cell (Source: Infineon)
The second subsystem includes a hydrogen distributor, through a very safe connection. The constant measurement of the flow avoids losses. The hydrogen is cooled to a temperature of about –40˚C to reach a high density in the tank. It then passes through the pressure regulator and to the high-speed injector, which will allow a recirculation of the material. It is necessary to avoid releasing hydrogen in the exhaust. In the third subsystem, the electrical voltage is continuously controlled. The fourth subsystem, the exhaust subsystem, involves a flow from the air system that is heavily loaded with water vapor. Sophisticated systems operate in an extremely silent way. The fifth subsystem is dedicated to thermal management. It controls and regulates the temperature of the water and prevents the formation of ice if the temperature is very cold. It is managed by powerful microcontrollers.
Conclusion
Green hydrogen can certainly be one of the solutions to solve the climate crisis, and there are many companies that are carrying out research in this direction. The biggest challenges are focused on the production, storage, transport, and use of green hydrogen, and many manufacturers are offering a broad portfolio of electronic products and components for the construction of electronic systems to produce and consume clean energy.
Reference
Power semiconductor solutions for the development of green hydrogen systems — Markus Hermwille,
Infineon Technologies AG, Nils Przybilla, Infineon Technologies Bipolar GmbH, Patrick Leteinturier,
Infineon Technologies AG — Webinar