High-voltage fast charging for electric vehicles has become the key to promoting market development. Silicon carbide (SiC) technology has a high breakdown field strength, low on-state resistance, and off-state leakage current, which meets the needs of electric vehicles. This article will show you the current fast charging development trends of the electric vehicle market and vehicle-to-grid (V2G) applications, as well as SiC solutions from Wolfspeed.
High voltage charging technology improves charging speed and efficiency
Customers who are used to driving internal combustion engine vehicles which can run up to 400 miles at a time will inevitably have “range anxiety” about electric vehicles. However, with the increases in battery capacity and the improvement of battery management technology, the latest electric vehicles have reached a cruising range of about 200 miles, and it is expected that 300 miles will soon become popular. At present, there are already models with cruising ranges exceeding 400-500 miles on the market, and the problem of “range anxiety” will be alleviated accordingly.
However, with increases in the battery capacity of electric vehicles, the speed and efficiency of battery charging will become more important. In order to promote the sustainable growth of the electric vehicle market, a charging infrastructure with shorter charging times is needed, and 80% of the capacity must be filled in 12 to 15 minutes. This demand can safely achieve the higher power output required by such fast chargers by increasing the voltage.
Charging with a high voltage has many advantages. High voltage brings lower current, thus reducing power loss in cables and battery overheating, and maintaining power better. It can also reduce the weight, because the reduced cable size requires less copper, thus reducing the required space and weight. Smaller cable size also helps to reduce the cost caused by expensive copper cables and connectors.
A number of new models have started using 800V or 900V DC fast charging technology. However, with a high-voltage solution, electric vehicle companies will need to make major changes to everything, including increasing the number of winding turns of the motor, enhancing the insulation of conductors, and redesigning the main power circuit, so as to using the leading-edge power components with a withstand voltage higher than 800 V.
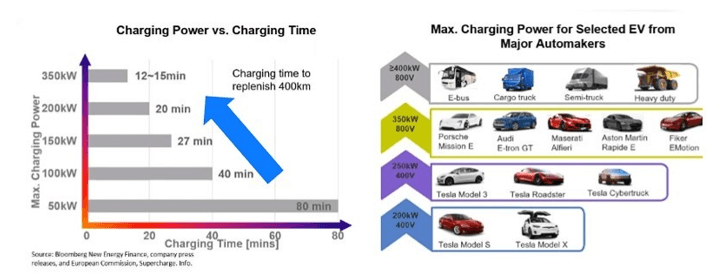
(Sources: YOLE DÉVELOPPEMENT, POWER SIC MATERIALS, DEVICES AND APPLICATIONS 2020)
V2G improves energy efficiency
On the other hand, another important trend that chargers must support is V2G. The so-called V2G describes the relationship between electric vehicles and the power grid. When electric vehicles are not in use, the electric energy of on-board batteries can be sold to the power grid system, and when on-board batteries need to be charged, the current flows from the power grid to vehicles.
With each company creating an important business model for the powerful on-board energy storage system (ESS), V2G is developing gradually. Although solar energy and stationary ESS will definitely play an important role in the future of electrification, V2G function is highly expected when dealing with peak load.
Given that large-scale commercial and industrial energy consumers must pay more for the required peak power and higher average power factor, and bidirectional DC fast chargers can switch the function of charging electric vehicles to supplying power to enterprise sites or power grids during peak load, it provides an attractive economic case for installing the system.
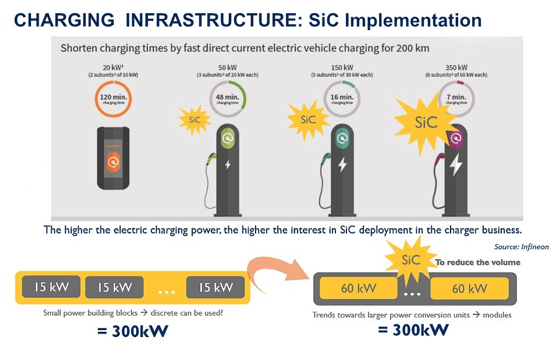
(Sources: YOLE DÉVELOPPEMENT, POWER SIC MATERIALS, DEVICES AND APPLICATIONS 2020)
SiC devices have many advantages over silicon-based devices
Compared with silicon (Si) devices, SiC devices provide many advantages, like the breakdown field strength of SiC being ten times higher than silicon, so the blocking voltage on a smaller bare die area is higher than that of silicon. At present, SiC can support a MOSFET blocking voltage as high as 1700V, while a silicon-based super junction MOSFET is usually below 900V.
Compared with silicon, SiC has lower on-state resistance and off-state leakage current, so it is helpful for improving efficiency. SiC has very low or even no reverse recovery current, and can switch at a frequency three to five times higher than that of silicon, thus reducing the size and weight of capacitors and magnetic components. In addition, SiC has a thermal conductivity which is three times higher and can withstand higher chip temperatures, thus reducing the cooling requirements.
These characteristics give 1200V SiC devices significant cost/performance advantages over silicon-based insulated gate bipolar transistors (IGBT), and provide higher efficiency, thermal profiles, and power density needed to realize the architecture of 800V to 900V electric vehicles.
Both on-board chargers and charging piles contain two main modules, including an active front end (AFE) for AC/DC conversion and DC/DC converters. The AFE obtains single-phase or three-phase power from the power grid, and then outputs it to the DC intermediate voltages, and then converts it into the voltage required by the fast charging of the battery of the electric vehicle through the DC/DC module.
The other module is an on-board charger (OBC), which usually uses a single module of 3 kW to 11 kW. The charging pile is made of modules ranging from 15 kW to 30 kW, and the stack combination achieves a 150 kW current and the latest target is 350 kW. With the latest SiC devices, packages and circuit topologies, this goal can be achieved with fewer 60 kW modules in the near future.
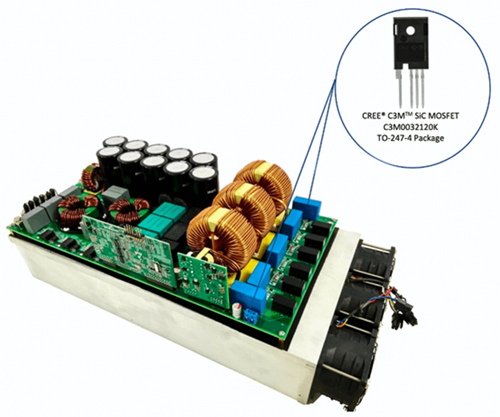
Enriching product mix and reference design to speed up development
Wolfspeed provides the key component to support the rich product portfolio of a 1200V MOSFETs and Schottky diodes in the electric vehicle market. Wolfspeed’s 1200 V blocking voltage third generation (C3M) MOSFET series has a rated current range of 7.2A to 115A, an on-resistance (RDSon) of 350 mΩ to 16 mΩ, and a maximum junction temperature of 150℃ or 175℃. These devices are available in standard TO-247-3 and optimized TO-247-4 and TO263-7 packages, and their Kelvin source pin connections can help optimize the performance of these ultrafast SiC devices.
Wolfspeed also provides reference designs, which can simplify the design work and shorten the time to market. In response to the latest trend of electric vehicle chargers, Wolfspeed has developed a 22kW solution, which includes an AFE and a flexible DC/DC converter, which can be used for both on-board chargers and power modules for DC fast chargers.
The combination of the two reference design boards is very unique, supporting bidirectional single-phase and three-phase operation, meeting the needs of fixed battery voltage in on-board chargers, and variable voltage from 200V to 800V for DC fast chargers to serve both previous generation electric vehicles and 800V electric vehicles. The flexibility of AFE and DC/DC design opens up new opportunities for engineers to target applications other than electric vehicles, such as ESS, UPS, and other industrial power conversion systems.
The CRD-22AD12N AFE operating at 45kHz uses a simple six-switch topology. Although the switches can support higher frequencies, there is a trade-off between induced core loss and switching efficiency. This topology can directly replace similar 6-IGBT circuits. IGBT solutions are simple and inexpensive, but because of the existence of IGBT tail current, switching loss and high efficiency are low, and its frequency is as low as 20 kHz.
A CRD-22DD12N DC/DC board is equipped with a full-bridge CLLC resonant converter with a flexible control scheme, which realizes frequency modulation, phase shift control, adaptive synchronous rectification, and bridge reconfiguration technique. Its topology realizes zero-voltage turn-on and low-current turn-off, which leads to lower switching loss and lower electromagnetic interference (EMI). All these implementations are accompanied by fewer power devices and lower system costs. Combining an AFE and DC/DC board brings significant advantages over silicon-based solutions.
Conclusion
With the battery voltage of electric vehicles moving towards 800 V, the 1200 V SiC switch not only can realize the new electric vehicle architecture with a target charging time of 15 minutes, but also open a new opportunity for the application of bi-directional chargers in V2G. Wolfspeed provides engineers with a CRD-22DD12N DC/DC reference board for the design of CRD-22AD12N AFE, which shows many advantages of adopting SiC devices compared with silicon devices, including reducing overall system cost, weight and size, improving system efficiency, simplifying thermal dissipation design and cost burden, etc. It can also simplify power supply system design to shorten the time to market, and will be an ideal choice for developing high voltage charging applications.