At a time when aerospace design subsystems are becoming increasingly smaller, more powerful and more complex, thermal management can no longer be an afterthought. Especially, when aerospace applications tend to generate excessive heat, thermal management issues need to be addressed at the very beginning of the design process.
The next-generation commercial aircraft is likely to require far more power than today's airplanes, so for processing-intensive aerospace applications, thermal management may be an even bigger concern than generating power.
Moreover, thermal management design limitations are intertwined with size, weight, and power consumption (SWaP) constraints in aerospace embedded systems and RF monolithic microwave integrated circuits (MMICs). So, if design engineers can reduce the size of cooling systems in power supplies, the impact will go all the way as a lower bill-of-materials (BOM) cost can lead to less thermal management requirements.
It’s worth mentioning that when it comes to thermal management, there are multiple dimensions, spanning from cold plates that act as a liquid-cooled enclosure to a plumbing system that moves the liquid and vapor to where the heat exchanger is located. Then there are heat sinks that dissipate the heat.
However, this article will focus on how the right selection of components and system-level design know-how enable developers to create the right thermal management solution for extreme conditions in commercial aviation. It will also show how system engineers can enhance the performance of RF power amplifiers (PAs) and deeply embedded aircraft systems by limiting the amount of heat dissipation.
Thermal Management with SiC and GaN
Thermal management is now far more crucial at the component level because ever-smaller chip geometries generate more heat within the same-size footprint. More heat, in turn, slows processor speeds, particularly at chip hotspots, where heat concentrates and temperatures soar.
However, at a time when the issue of heat management is reaching a bottleneck, wideband gap (WBG) semiconductors such as silicon carbide (SiC) and gallium nitride (GaN) come to the rescue by significantly improving system efficiency and power density in aerospace applications. A semiconductor material that can get heat out of the die quickly is a boon for aerospace electronics that places multiple devices in close proximity and generates kilowatts of heat.
For a start, the SiC and GaN devices allow power designs to move from active to passive cooling because the thermal conductivity of WBG materials is much better. That enables power system designers to replace liquid cooling systems. Next, a boost in switching frequency reduces the system size and the overall number of magnets and capacitors. It also reduces the amount of metal in heatsinks and enclosures.
In other words, better thermal management means that fewer support components are needed, which also means that there are fewer parts to break. The lighter power supplies, for instance, require smaller magnets and thus reduce the size of heatsinks. They can even eliminate heatsinks in some cases.
The stable operability of SiC and GaN devices at higher temperatures is especially critical for avionic designs with SWaP constraints. These broadband power devices lead to lighter-weight subsystems that lower fuel consumption and heat emissions for the aerospace industry. Not surprisingly, therefore, the aerospace designs are increasingly moving toward SiC and GaN semiconductor solutions to reduce the size of power converters for the amount of load they have to carry.
The WBG material’s ability to complement high power density with high thermal conductivity enables the SiC and GaN devices to dissipate heat more efficiently than other chip technologies. That allows these semiconductor devices to operate at lower temperatures at a given output power, leading to greater reliability, higher breakdown voltages, and higher Mean Time Between Failure (MTBF) compared to GaAs and silicon devices (Figure 1).
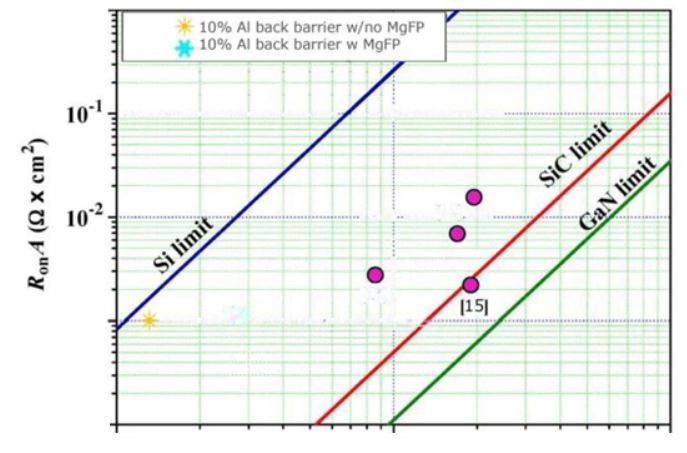
Figure 1: A comparison of breakdown voltage ratings for silicon, SiC, and GaN devices. Image source: Research Gate
SiC MOSFETs for Avionics Power
The aviation industry is starting to recognize the potential benefits of SiC semiconductors for power supply system. For example, SiC MOSFETs with low on-state resistance lead to lower conduction losses and minimal impact of temperature variations. That translates into less thermal management, which in turn, means smaller and more economical heatsinks and fewer costly cooling parts.
The SiC MOSFETs promise to significantly reduce the size and weight of avionic power switches, facilitating substantial reductions in fuel consumption and heat emissions. Their high thermal conductivity and high resistance to electric field breakage ensure embedded thermal management to enhance aerospace electronics’ performance.
Take the example of MSC040SMA120B, the 1,200-V SiC MOSFET from Microsemi, a Microchip subsidiary. It promises more effective thermal management in power distribution, actuation, air conditioning, and motor control applications in aerospace designs.
For SiC devices employed in power distribution and motor drive applications, the management of the gate drive conditioning circuit has become a crucial challenge. The MSC040SMA120B SiC MOSFETs feature high channel mobility, oxide lifetime, and threshold voltage stability to respond to this challenge.
Microchip has also incorporated the MSC040SMA120B SiC MOSFETs in its MSCSICMDD/REF1 reference design board for switch-configurable high/low-side driver with half bridges or independent drive (Figure 2). MSCSICMDD/REF1, a highly-isolated SiC MOSFET dual-gate driver, can be configured by switches to drive as a half-bridge configuration with one side on and dead time protection.
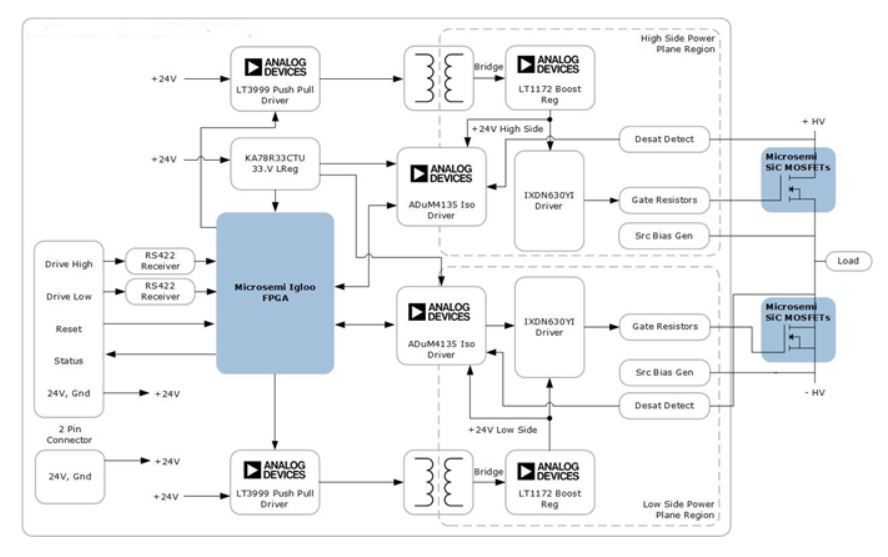
Figure 2: The reference design facilitates a highly-isolated SiC MOSFET dual-gate driver switch to provide a means for evaluating SiC MOSFETs in several topologies. Image source: Microchip
GaN for Power Amplification
GaN devices, like SiC semiconductors, can tolerate a much higher operating temperature and feature high thermal conductivity and breakdown voltage. Furthermore, GaN semiconductor can be grown on a SiC substrate rather than on its own. The higher thermal conductivity of SiC substrates favors the GaN-on-SiC devices in serving the high-voltage and high-power applications common in commercial aerospace designs.
Take, for instance, the 65-V GaN technology, which is triggering a new generation of radar systems that open new design opportunities in a wide range of commercial aviation applications. Here, GaN high-electron-mobility transistor (HEMT) devices on SiC substrates offer smooth heat dissipation for long-term reliability.
Wolfspeed’s CGHV96100F2, a GaN HEMT manufactured on SiC substrates, features high breakdown voltage, high saturated electron drift velocity, and high thermal conductivity (Figure 3). Additionally, it’s available in metal- or ceramic-flanged package to boost electrical and thermal performance.
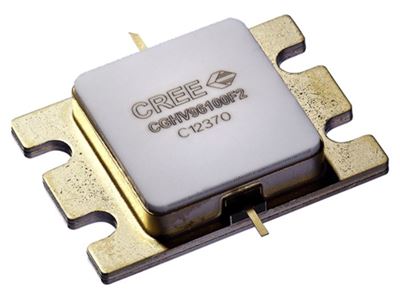
Figure 3: The GaN transistor supports the output power of 100 watts and operating frequency ranging from 7.9 GHz to 9.6 GHz.
Image source: Wolfspeed
GaN devices—HEMTs and MMICs—are becoming popular in aerospace designs like avionic radars because they provide a smooth way to increase the RF power by increasing the voltage on PAs as compared to silicon-germanium (SiGe), gallium arsenide (GaAs), and silicon-based lateral diffusion MOSFET (LDMOS) technologies.
Aircraft designs are increasingly implementing higher-power PAs into payloads and wing tips with stringent thermal management requirements. Besides facilitating higher voltage and power amplification, GaN devices are also crucial in developing lightweight solutions, critical in space-constrained aviation designs.
Conclusion
The need for higher density inevitably calls for significant cooling improvements in aerospace embedded systems. The space-conscious aerospace industry is also demanding lighter designs that inevitable ease thermal management challenges.
As shown in this article, SiC and GaN devices fit the bill when it comes to complex thermal management challenges in avionic embedded systems. However, these WBG devices are still in an early stage, and they aren’t yet fully commoditized. So, aerospace system designers have to be mindful in selecting components to ensure that devices they choose meet their specific thermal management requirements.