Industrial networks are crucial to the working of a plant or factory. With thousands of end nodes aggregated for control and monitoring, often operating under harsh environments, the industrial network is characterized by strict requirements for connectivity and communication.
Industrial Connectivity for IIoT
Industrial network protocols form the basis for communication between industrial network devices and a large number of industry specific network protocols have been developed over the past decades, each designed for specific purposes and environments. The figure below outlines the key application domains and the plethora of protocols available today in these domains. The emergence of the Industrial Internet of Things (IIoT) and new possibilities for connectivity with wireless and Ethernet are changing the protocol landscape. New value in integrating public and private enterprise clouds, operational systems and business domains is presenting new opportunities for protocol harmonization in industrial environments.
In this primer we examine the key protocols used in industrial environments and also assess the emerging trends that constitute the evolution of these protocols to support next generation industrial settings.
Industrial Network Protocols
Fundamental to the industrial protocol landscape are the various layers of data acquisition and aggregation in the industrial communication network. Typical networks in industrial settings have four layers:
1. Field Layer – This layer constitutes a large numbers of sensor, transducer and actuator nodes. The sensor/transducer nodes are typically collecting environmental or process control information and relaying them back to controllers or for monitoring. Actuators implement instructions received from controllers as physical motor-actions in the field equipment.
2. Control Layer – Logic controllers, which can be distributed or centralized, aggregate the sensor/actuator data and transmit the same to larger scale plant control systems. Programmable Logic Controllers (PLCs) or Distributed Control Systems (DCS) also provide local control typically to specific domain groups in the plant. They execute various types of machines or process instructions such as logic, sequencing, timing, counting and arithmetic to control through digital or analog modules.
3. Supervisory Layer – This layer includes plant control systems with human-machine interfaces to drive plant operations. Supervisory Control and Data Acquisition (SCADA) systems report to human operators, offer continuous remote monitoring of alerts and provide a comprehensive view of the entire managed system. Key functions in this layer also include data processing, logging and historical trending.
4. Execution and Planning Layer – performs the manufacturing and engineering execution. Resource and equipment scheduling, Work in Progress (WIP) job specifications and general work planning are performed and executed by Manufacturing Execution Systems (MES). This layer is the interface between business priorities and operational systems. Enterprise and planning related functions such as demand planning, procurement, forecast management and inventory are crucial functions driven by Enterprise Resource Planning (ERP) systems at this layer.
Network Protocol Hierarchies
The protocol and connectivity requirements vary across the network hierarchy based on application need, reliability requirements, bandwidth, etc. The choice of protocol is driven by considering several factors:
• End Node Power: End nodes constituting sensors and actuators are crucial inputs into the plant control system and need to be continuously powered. Both battery power and power from mains is employed. Since some protocols consume more power than others, access to power can eliminate or facilitate their use. For example, Wi-Fi has a high power requirement and is often not well suited for remote nodes that are battery powered and the cost of frequently replacing batteries can be prohibitive.
• Wiring: Modern plants can span several square kilometres and installation long lengths of wire to connect up end nodes is often an expensive proposition. The problem can be even more acute when sensor nodes are in hard to reach positions like a CO2 sensor on a flue. Wireless protocols can be better suited for such needs when power requirements can be effectively met. Also, the intermediate control points (PLCs) can be located closer to the end-nodes to save on wiring. Since the protocols are often different between the control layer and sensor layer, protocol choice can be impacted by the degree of intermediate control in the plant.
• Operating Conditions: Industrial infrastructure and equipment are often exposed to the elements and corrosive environments. In addition, safety and hazard tolerances are stringent and require special consideration. Protocols that can withstand the demands of these environments without compromising reliability of communications are crucial. Optimal operating temperature ranges, impact of vibrations and noise, susceptibility to interference and deterioration impact of humidity all are important factors in protocol choice.
• Packet Loss Rate: Some protocols are more resilient than others in ensuring minimal data degradation due to transmission issues like congestion, bit errors or bad connectivity. While some data loss is not harmful for non-critical applications or nodes, critical applications like reactor cores require transmission with no data loss.
• Throughput: The type and size of data transmissions can greatly impact protocol choice. Simple binary data that communicate on/off status can make do with low-cost, low-throughput protocols. However, image data from cameras requires protocols that allow for a much greater data volumes.
• Real-time/Deterministic: Some industrial applications cannot tolerate any delay in communications. Protocols that are not real-time and that cannot ensure that data packets are delivered immediately simply are unsuitable to meet the demands. This consideration is often cited for not using typical computer protocols like TCP/IP in industrial settings.
• Network Range, Load & Architecture: The distances data has to travel in the network, the number of nodes in the network and the network architecture itself can make a big difference in protocol choice. Network congestion, throughput and data loss can all become prominent in certain network architecture. Choosing the wrong protocol can be the difference between an efficient plant and one that is prone to problems.
• Security: Industrial networks need safeguards against both unintentional and malicious threats. Unlike website and other IT outages, the impact of security breaches cannot just be measured in financial and reputation damages. Human safety and national security can be threatened when networks without adequate protections like encryption are compromised.
• Scalability & Extensibility: An important factor is also the degree of scalability and extensibility that is needed. When new nodes need to be added frequently or the network configurations need change, some implementations can be expensive. Also, some networks like ZigBee can be architected to be self-organizing and self-healing on failure, making addition of new nodes or removal of new nodes fast and cheap.
All the above factors come into play regardless of the layer of the network, although general purpose protocols are more applicable in the higher layers with lower latency and real time requirements.
Industrial Network Protocol Landscape
The stringent demands of industrial networks have historically driven the creation of a wide variety of proprietary and application specific protocols. Wired and wireless networks each have their own protocol sets. Despite the large number of protocols that are available, most wired protocols adhere to two standards – Fieldbus or Industrial Ethernet. In recent times, wireless connectivity has shown the potential to reduce network costs and protocols like Wi-Fi, Cellular, Bluetooth, and ZigBee are all being used to varying degrees. Additionally, IO-Link, a serial point-to-point protocol is gaining popularity
in smart sensor type applications.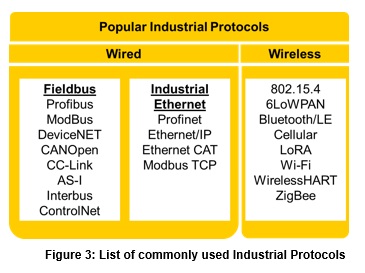
Fieldbus Applications
Fieldbus is a family of industrial computer network protocols used for real-time distributed control, standardized as IEC 61158. Fieldbus protocols eliminated the prior constraint where only two devices could communicate with each other over serial connections (like RS 232). By providing only one communications point at the controller level, hundreds of analog and digital nodes can communicate simultaneously using Fieldbus protocols. Daisy-chain, star, ring, branch, and tree type network topologies are all supported. The biggest benefit afforded by fieldbus has been the dramatic reduction of plant wiring. The table below summarizes the various protocols in the family and their characteristics. Advantages, disadvantages and application suitability are also presented. Salient characteristics of reliability and simplicity have made Fieldbus the protocol of choice of industrial networks.
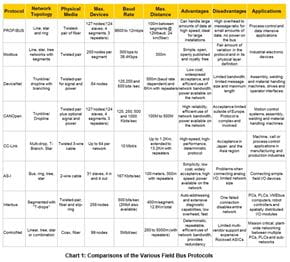
See related product
See related product
Industrial Ethernet: IIoT Solutions
This refers to the use of standard Ethernet protocols for automation or process control. Aided by rugged connectors and extended temperature switches to withstand rugged industrial settings, these protocols have seen widespread deployment particularly when deterministic delivery is less stringent. The use of fibre Ethernet reduces the problems of electrical noise and provides electrical isolation to prevent equipment damage. Since data collisions are common in Ethernet protocols, industrial uses of Ethernet employ full-duplex standards and other methods so that collisions do not unacceptably influence transmission times. The table below summarizes the various protocols in the family and their characteristics. Advantages, disadvantages and application suitability are also presented. The main drivers behind the growth of Ethernet are its higher performance and ability to integrate with office networks.
Wireless Network Protocols: Wireless Technology in Industrial Networks
Wireless has brought new opportunities to save on network operational costs and ease installation. While still in its early stages of adoption these protocols are increasingly considered as the future. Primary advantages are the elimination of wiring and the ability to drive more monitoring and control points. Today, sensors and measurement devices are the primary wireless protocol users. The most common wireless technologies for industrial automation include 802.11.x Wi-Fi, Bluetooth, Cellular, proprietary unlicensed ISM radio and 802.15.4 based protocols such as WirelessHART, ISA100.11a, WIA-PA and ZigBee. Wi-Fi adoption typically accompanies Industrial Ethernet deployments and often coexists as a second backbone for communications. Bluetooth is being used as a point-to-point wire-replacement, for example, between an HMI solution and a field device. Cellular connectivity is typically used for backhaul communication between plants, connecting remote devices in long haul SCADA applications and for third party access to machinery and robots. The table below summarizes the various protocols in the family and their characteristics. Advantages, disadvantages and application suitability are also presented. With new possibilities unleashed by data analytics and IoT, wireless protocols will continue their growth in the industrial setting.
Network Connectivity Advancements
Fieldbus based protocol solutions that have been around for decades represent the bulk of the protocols currently in use. Analysts estimate that between 55-65% of all industrial connectivity is afforded by Fieldbus technologies and the annual rate is about 7%. Industrial Ethernet connectivity has reached mainstream and is being increasingly adopted. Ethernet nodes are expected to outpace the growth in traditional connectivity. However, the rate of adoption has been slower than expected – largely due to the safety, resilience and tradition that Fieldbus brings. In general, industrial stakeholders are hesitant to drive rapid change in their environments as failure can be catastrophic. Ethernet penetration hovers around 30-40% in most forecasts with a growth rate in the 20% range. The installed base of wireless devices in industrial applications is 4% and is forecasted to grow at a compound annual growth rate of 30%. Most of the major vendors of wireless IoT devices in industrial automation offer a wide range of solutions with various wireless technologies in order to support many different applications.
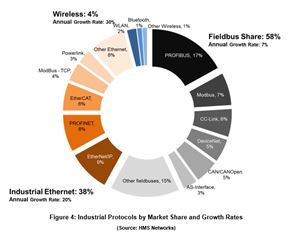
Common Network Connectivity Devices
As smarter low-cost devices proliferate and the digital convergence afforded by modern Ethernet protocols increases in value, it is widely expected that Ethernet, and Wireless along with it, will experience greater adoption. IoT, pervasive sensing and data growth represent the greatest propellers of change in the industry. The potential to monitor every individual control and monitoring point and the ability to gather large amounts of data to feed advanced preventative maintenance schemes are of great interest to industry practitioners. Of particular importance is the integration value of enterprise systems and operational systems. Most enterprises are harnessing cloud (public and private) operating models to drive down the total cost of ownership of their IT infrastructure. It is likely that the cloud paradigm will also see adoption in next generation control systems. Current limitations on data throughputs and security will no longer suffice as new strategies predicated on collecting vast amounts of data gain prominence.
While it is hard to predict the death of one technology over the other, the huge install base of Fieldbus devices and its accompanying community of experts indicate a future where Ethernet, Fieldbus and Wireless technologies coexist for many years to come.