Le reti industriali sono fondamentali per il funzionamento di un impianto o di una fabbrica. Con migliaia di nodi finali aggregati per il controllo e il monitoraggio, spesso operanti in ambienti difficili, la rete industriale è caratterizzata da rigidi requisiti di connettività e comunicazione.
I protocolli di rete industriali costituiscono la base per la comunicazione tra i dispositivi di rete industriali e negli ultimi decenni sono stati sviluppati numerosi protocolli di rete specifici per il settore, ciascuno progettato per scopi e ambienti specifici. La figura seguente illustra i principali domini di applicazione e la pletora di protocolli oggi disponibili in questi settori. L'emergere dell'Industrial Internet of Things (IIoT) e le nuove possibilità di connettività con il wireless e l'Ethernet stanno cambiando lo scenario dei protocolli. Il nuovo valore dell'integrazione tra cloud aziendali pubblici e privati, sistemi operativi e domini di business offre nuove opportunità per l'armonizzazione dei protocolli in ambienti industriali.
In questo manuale di base si esaminano i protocolli chiave utilizzati in ambienti industriali e si valutano le tendenze emergenti che costituiscono l'evoluzione di questi protocolli per supportare i contesti industriali di prossima generazione.
Rete industriale
Fondamentali per il panorama dei protocolli industriali sono i vari livelli di aggregazione e acquisizione dati nella rete di comunicazione industriale. Le reti tipiche in ambito industriale hanno i quattro livelli riportati di seguito.
1. Livello di campo: questo livello costituisce un gran numero di nodi sensori, trasduttori e attuatori. I nodi sensore/trasduttore in genere raccolgono informazioni ambientali o di controllo del processo e le ritrasmettono ai controller per il monitoraggio. Gli attuatori implementano le istruzioni ricevute dai controller come azioni motorie fisiche nell'apparecchiatura di campo.
2. Livello di controllo: i controller logici, che possono essere distribuiti o centralizzati, aggregano i dati dei sensori/attuatori e li trasmettono ai sistemi di controllo dell'impianto su larga scala. I controller a logica programmabile (PLC) o i sistemi di controllo distribuito (DCS) forniscono anche il controllo locale di gruppi di domini specifici nell'impianto. Eseguono vari tipi di macchine o istruzioni di processo, quali logica, sequenziamento, temporizzazione, conteggio e aritmetica da controllare tramite moduli digitali o analogici.
3. Livello di supervisione: questo livello comprende sistemi di controllo dell'impianto con interfacce uomo-macchina per gestire le operazioni dell'impianto. I sistemi SCADA (Supervisory Control and Data Acquisition) riportano agli operatori umani, offrono un monitoraggio remoto continuo delle notifiche e forniscono una visione completa dell'intero sistema gestito. Le funzioni chiave di questo livello includono anche l'elaborazione dei dati, la registrazione e i trend storici.
4. Livello di esecuzione e pianificazione: consente l'esecuzione di produzione e progettazione. La programmazione delle risorse e delle attrezzature, le specifiche di lavoro in corso (WIP) e la pianificazione generale del lavoro sono eseguite dai sistemi di esecuzione della produzione (MES, Manufacturing Execution Systems). Questo livello è l'interfaccia tra le priorità aziendali e i sistemi operativi. Le funzioni relative all'impresa e alla pianificazione, come la pianificazione della domanda, l'approvvigionamento, la gestione delle previsioni e l'inventario, sono funzioni fondamentali guidate dai sistemi ERP (Enterprise Resource Planning) in questo livello.
I requisiti di protocollo e connettività variano da una gerarchia di rete all'altra in base alle esigenze delle applicazioni, ai requisiti di affidabilità, all'ampiezza di banda e così via. La scelta del protocollo è guidata dalla considerazione di diversi fattori:
• Potenza del nodo finale: i nodi finali che costituiscono i sensori e gli attuatori sono ingressi cruciali nel sistema di controllo dell'impianto e devono essere alimentati in modo continuo. Viene utilizzata sia l'alimentazione a batteria che dalla rete elettrica. Poiché alcuni protocolli consumano più energia di altri, l'accesso all'alimentazione può eliminarne o facilitarne l'utilizzo. Ad esempio, il Wi-Fi ha requisiti di alta potenza e spesso non è adatto per i nodi remoti alimentati a batteria e il costo della sostituzione frequente delle batterie può essere proibitivo.
• Cablaggio: gli impianti moderni possono estendersi per diversi chilometri quadrati e l'installazione di cavi molto lunghi per collegare i nodi finali è spesso costosa. Il problema può essere ancora più accentuato quando i nodi dei sensori si trovano in posizioni difficili da raggiungere, come un sensore di CO2 su una canna fumaria. I protocolli wireless possono essere più adatti a tali esigenze quando i requisiti di alimentazione possono essere soddisfatti in modo efficace. Inoltre, i punti di controllo intermedi (PLC) possono essere posizionati più vicino ai nodi finali per limitare la lunghezza del cablaggio. Poiché i protocolli sono spesso diversi tra il livello di controllo e il livello sensori, la scelta del protocollo può essere influenzata dal grado di controllo intermedio nell'impianto.
• Condizioni di funzionamento: le infrastrutture e le attrezzature industriali sono spesso esposte agli agenti atmosferici e agli ambienti corrosivi. Inoltre, le tolleranze di sicurezza e di pericolo sono rigide e richiedono una particolare considerazione. I protocolli in grado di soddisfare le esigenze di questi ambienti senza compromettere l'affidabilità delle comunicazioni sono fondamentali. Intervalli di temperatura d'esercizio, impatto di vibrazioni e rumori, suscettibilità alle interferenze e impatto di deterioramento dell'umidità sono tutti fattori importanti nella scelta del protocollo.
• Tasso di perdita del pacchetto: alcuni protocolli sono più resistenti di altri nel garantire il minimo degrado dei dati a causa di problemi di trasmissione come congestione, errori di bit o connettività insufficiente. Sebbene alcune perdite di dati non siano dannose per le applicazioni o i nodi non critici, le applicazioni critiche come i nuclei dei reattori richiedono la trasmissione senza perdita di dati.
• Velocità di elaborazione: il tipo e la dimensione delle trasmissioni di dati possono avere un notevole impatto sulla scelta del protocollo. Per i dati binari semplici che comunicano lo stato on/off possono essere sufficienti protocolli a basso costo e a bassa velocità di elaborazione. Tuttavia, i dati delle immagini provenienti dalle telecamere richiedono protocolli che consentono volumi di dati molto maggiori.
• Comportamento in tempo reale/deterministico: alcune applicazioni industriali non possono tollerare alcun ritardo nelle comunicazioni. I protocolli che non sono in tempo reale e che non possono garantire la consegna immediata dei pacchetti di dati sono semplicemente inadatti a soddisfare le esigenze. Questa considerazione viene spesso menzionata per dissuadere dall'utilizzo di protocolli di computer tipici come TCP/IP in ambienti industriali.
• Gamma di rete, carico e architettura: le distanze che i dati devono percorrere nella rete, il numero di nodi nella rete e l'architettura di rete stessa possono fare una grande differenza nella scelta del protocollo. La congestione della rete, la velocità di elaborazione e la perdita di dati sono tutti fattori che possono diventare importanti in alcune architetture di rete. La scelta del protocollo sbagliato può fare la differenza tra un impianto efficiente e uno che è soggetto a problemi.
• Sicurezza: le reti industriali devono essere protette sia contro le minacce involontarie che contro quelle dannose. A differenza delle interruzioni dei siti Web e di altri sistemi IT, l'impatto delle violazioni della sicurezza non può essere misurato solo in termini di danni finanziari e di reputazione. La sicurezza delle persone e quella nazionale possono essere minacciate quando reti senza protezioni adeguate come la crittografia vengono compromesse.
• Scalabilità ed estensibilità: un fattore importante è anche il grado di scalabilità ed estensibilità necessario. Quando è necessario aggiungere nuovi nodi frequentemente o modificare le configurazioni di rete, alcune implementazioni possono essere costose. Inoltre, alcune reti come ZigBee possono essere progettate per l'organizzazione automatica e la risoluzione automatica dei problemi, rendendo l'aggiunta o la rimozione di nuovi nodi veloce ed economica.
Tutti i fattori riportati precedentemente entrano in gioco indipendentemente dal livello della rete, anche se i protocolli per scopi generici sono più adatti ai livelli superiori con requisiti di latenza e tempo reale più bassi.
Panorama dei protocolli industriali
I rigidi requisiti delle reti industriali hanno storicamente promosso la creazione di un'ampia varietà di protocolli proprietari e specifici per le applicazioni. Le reti cablate e wireless hanno ciascuna un proprio set di protocolli. Nonostante il gran numero di protocolli disponibili, la maggior parte dei protocolli cablati aderisce a due standard: Fieldbus o Ethernet industriale. Negli ultimi tempi, la connettività wireless ha mostrato il potenziale di ridurre i costi di rete e protocolli come Wi-Fi, Cellular, Bluetooth e ZigBee sono tutti utilizzati in varia misura. Inoltre, IO-Link, un protocollo seriale punto-punto sta acquisendo popolarità
in applicazioni tipo di sensore smart.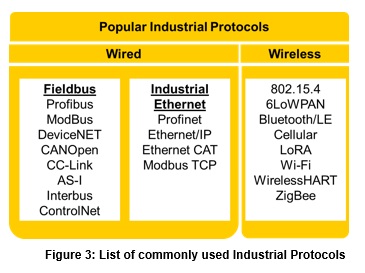
Fieldbus
Fieldbus è una famiglia di protocolli di rete per computer industriali utilizzati per il controllo distribuito in tempo reale, standardizzati come IEC 61158. I protocolli Fieldbus hanno eliminato il vincolo precedente, in base al quale solo due dispositivi potevano comunicare tra loro tramite connessioni seriali (come RS 232). Fornendo un solo punto di comunicazione a livello di controller, centinaia di nodi analogici e digitali possono comunicare simultaneamente utilizzando i protocolli Fieldbus. Sono supportate tutte le topologie di rete a catena, a stella, ad anello, a diramazione e ad albero. Il maggior vantaggio offerto dal bus di campo è stata la drastica riduzione del cablaggio dell'impianto. La tabella seguente riassume i vari protocolli della famiglia e le relative caratteristiche. Vengono inoltre indicati vantaggi, svantaggi e idoneità all'applicazione. Caratteristiche salienti di affidabilità e semplicità hanno reso Fieldbus il protocollo preferito per le reti industriali.
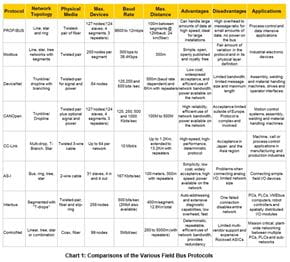
Visualizza prodotti correlati
Visualizza prodotti correlati
Ethernet industriale
Protocolli wireless
Il wireless ha offerto nuove opportunità per risparmiare sui costi operativi della rete e facilitare l'installazione. Pur essendo ancora in fase iniziale di adozione, questi protocolli sono sempre più considerati una soluzione valida per il futuro. I vantaggi principali sono l'eliminazione del cablaggio e la possibilità di gestire un maggior numero di punti di monitoraggio e controllo. Oggi, i sensori e i dispositivi di misurazione sono i principali fruitori del protocollo wireless. Le più comuni tecnologie wireless per l'automazione industriale includono 802.11.x Wi-Fi, Bluetooth, Cellular, radio ISM proprietaria senza licenza e protocolli basati su 802.15.4 come WirelessHART, ISA100.11a, WIA-PA e ZigBee. L'adozione del Wi-Fi di solito accompagna l'implementazione dell'Ethernet industriale e spesso coesiste come seconda spina dorsale per le comunicazioni. Il Bluetooth viene utilizzato come sostituzione dei cavi punto-punto, ad esempio, tra una soluzione HMI e un dispositivo di campo. La connettività cellulare è in genere utilizzata per la comunicazione backhaul tra impianti, per la connessione di dispositivi remoti in applicazioni SCADA a lungo raggio e per l'accesso di terzi a macchinari e robot. La tabella seguente riassume i vari protocolli della famiglia e le relative caratteristiche. Vengono inoltre indicati vantaggi, svantaggi e idoneità all'applicazione. Con le nuove possibilità offerte dall'analisi dei dati e dall'IoT, i protocolli wireless continueranno a crescere nel contesto industriale.
Evoluzione del mercato
Le soluzioni di protocollo basate su Fieldbus esistenti da decenni rappresentano la maggior parte dei protocolli attualmente in uso. Gli analisti stimano che il 55-65% di tutta la connettività industriale è offerta dalle tecnologie Fieldbus e il tasso annuo è di circa il 7%. L'Ethernet industriale è la tecnologia dominante ed è sempre più adottata. Si prevede che i nodi Ethernet superino la crescita della connettività tradizionale. Tuttavia, il tasso di adozione è stato più lento del previsto, in gran parte a causa della sicurezza, della resilienza e della tradizione ai quali è associato Fieldbus. In generale, le parti interessate del settore industriale esitano a promuovere un rapido cambiamento del loro ambiente, in quanto un fallimento può essere catastrofico. Nella maggior parte delle previsioni, la penetrazione dell'Ethernet si aggira intorno al 30-40%, con un tasso di crescita del 20%. La base installata di dispositivi wireless nelle applicazioni industriali è del 4% e si prevede che aumenti a un tasso di crescita annuo composto del 30%. La maggior parte dei principali venditori di dispositivi IoT wireless nell'automazione industriale offre una vasta gamma di soluzioni con varie tecnologie wireless al fine di supportare molte applicazioni diverse.
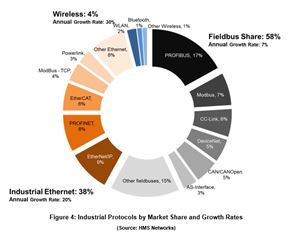
Con la proliferazione di dispositivi più intelligenti a basso costo e l'aumento del valore della convergenza digitale offerta dai moderni protocolli Ethernet, si prevede una maggiore adozione dell'Ethernet, e con esso del wireless. L'IoT, il rilevamento pervasivo e la crescita dei dati rappresentano i maggiori fattori del cambiamento del settore. La possibilità di monitorare ogni singolo punto di controllo e monitoraggio e la capacità di raccogliere grandi quantità di dati per alimentare schemi avanzati di manutenzione preventiva sono di grande interesse per gli operatori del settore. Di particolare importanza è il valore di integrazione dei sistemi aziendali e dei sistemi operativi. La maggior parte delle aziende utilizza modelli operativi cloud (pubblici e privati) per ridurre il costo totale di proprietà dell'infrastruttura IT. È probabile che il paradigma del cloud venga adottato anche nei sistemi di controllo di prossima generazione. Le attuali limitazioni su velocità di elaborazione e sicurezza non saranno più sufficienti in quanto le nuove strategie basate sulla raccolta di grandi quantità di dati acquisiranno maggiore importanza.
Sebbene sia difficile prevedere la fine di una tecnologia a favore di un'altra, l'enorme base installata di dispositivi Fieldbus e la relativa comunità di esperti indicano un futuro in cui Ethernet, Fieldbus e tecnologie wireless coesistono per molti anni a venire.