Las redes industriales son cruciales para el funcionamiento de una planta o una fábrica. Con miles de nodos terminales operados en conjunto para el control y el monitoreo, funcionando frecuentemente en entornos difíciles, la red industrial se caracteriza por sus requerimientos estrictos de conectividad y comunicación.
Los protocolos de red industrial conforman la base de la comunicación entre los dispositivos de redes industriales y se ha desarrollado un gran número de protocolos de red específicos del sector durante las últimas décadas, cada uno de ellos diseñado para un propósito y un entorno específico. La siguiente figura describe los dominios de aplicaciones clave y la gran variedad de protocolos que actualmente están disponibles en estos dominios. La aparición del Internet de las Cosas Industrial (IIoT) y las nuevas posibilidades de conectividad inalámbrica y Ethernet están cambiando el panorama de los protocolos. El nuevo valor de la integración de las nubes públicas y privadas empresariales, los sistemas operativos y los dominios empresariales está presentando nuevas oportunidades de armonización de protocolos en los entornos industriales.
En esta guía examinamos los protocolos clave utilizados en entornos industriales y evaluamos las tendencias emergentes que constituyen la evolución de estos protocolos para brindar soporte a la siguiente generación de configuraciones industriales.
La red industrial
Las diferentes capas de adquisición y agrupación de datos en la red de comunicación industrial son fundamentales para el panorama de protocolos industriales. Las redes típicas en configuraciones industriales tienen cuatro capas:
1. Capa de campo: esta capa constituye un gran número de nodos de sensor, transductor y actuador. Los nodos de sensor/transductor normalmente recopilan información de control del entorno o proceso y la envían de regreso a los controladores o se utiliza para el monitoreo. Los actuadores implementan instrucciones recibidas de los controladores como acciones motoras físicas en el equipo de campo.
2. Capa de control: los controladores lógicos, que se pueden distribuir o centralizar, agrupan los datos del sensor/actuador y los transmiten a los sistemas de control de mayor escala en las plantas. Los controladores lógicos programables (PLC, por sus siglas en inglés) o sistemas de control distribuidos (DCS) también proporcionan control local, normalmente para los grupos de dominios específicos de la planta. Estos ejecutan varios tipos de instrucciones para máquinas o procesos, como lógica, secuencia, coordinación, conteo y aritmética, para controlar por medio de módulos digitales o análogos.
3. Capa de supervisión: esta capa incluye los sistemas de control de la planta con interfaces humanas-automatizadas para impulsar las operaciones de la planta. Los sistemas de control de supervisión y adquisición de datos (SCADA, por sus siglas en inglés) envían informes a los operadores humanos, ofrecen un monitoreo remoto continuo de alertas y proporcionan una visión completa de todo el sistema administrado. Las funciones clave de esta capa también incluyen procesamiento de datos, registro y tendencias históricas.
4. Capa de ejecución y planeación: realiza la ejecución de fabricación e ingeniería. La programación de recursos y equipos, las especificaciones de trabajos en progreso (WIP, por sus siglas en inglés) y la planeación general del trabajo se realizan y ejecutan por medio de los sistemas de ejecución de fabricación (MES). Esta capa es la interfaz entre las prioridades empresariales y los sistemas operativos. Las funciones relacionadas con la empresa y la planeación, como planeación de demanda, aprovisionamiento, administración de pronósticos e inventarios, son funciones cruciales impulsadas por los sistemas de planeación de recursos empresariales (ERP, por sus siglas en inglés) en esta capa.
Los requisitos de protocolos y conectividad varían en las diferentes jerarquías de la red, según las necesidades de aplicación, los requerimientos de confiabilidad, el ancho de banda, etc. La elección del protocolo se realiza tomando en cuenta diferentes factores:
• Potencia del nodo de extremo: los nodos de extremo que constituyen sensores y actuadores son puntos de entrada cruciales para el sistema de control de la planta y se deben alimentar de forma continua. Se utiliza la energía de las baterías y la energía de los generadores principales. Debido a que algunos protocolos consumen más energía que otros, el acceso a la energía puede eliminar o facilitar su uso. Por ejemplo, el Wi-Fi tiene un requerimiento alto de energía y frecuentemente no es muy adecuado para los nodos remotos alimentados por baterías, además de que el costo de reemplazar las baterías frecuentemente puede ser prohibitivo.
• Cableado: las plantas modernas pueden abarcar varios kilómetros cuadrados y la instalación de grandes tramos de cables para conectar los nodos de extremo suele ser una propuesta costosa. El problema puede ser aún más grave cuando los nodos de sensor se encuentran en posiciones difíciles de alcanzar, como un sensor de CO2 en un tubo. Los protocolos inalámbricos pueden ser más aptos para estas necesidades cuando los requerimientos de energía se pueden cubrir de forma eficaz. Además, los puntos de control intermedios (PLC) se pueden ubicar más cerca de los nodos de extremo para ahorrar cableado. Debido a que los protocolos suelen ser diferentes entre la capa de control y la capa de sensor, la elección del protocolo se puede afectar por el grado de control intermedio que existe en la planta.
• Condiciones operativas: la infraestructura y el equipo industrial suelen estar expuestos a los elementos y a entornos corrosivos. Además, la seguridad y las tolerancias de riesgos son elementos rigurosos que suelen requerir una consideración especial. Los protocolos que pueden resistir las demandas de estos entornos sin sacrificar la confiabilidad de las comunicaciones son cruciales. Los diferentes rangos de temperatura de operación, el impacto de las vibraciones y el ruido, la susceptibilidad a interferencias y el impacto de deterioro causado por la humedad son factores importantes para la selección de un protocolo.
• Índice de pérdida de paquetes: algunos protocolos son más resistentes que otros para garantizar el desgaste mínimo de los datos debido a problemas de transmisión, como congestión, errores de bits o mala conectividad. Aunque en algunos casos la pérdida de datos no resulta dañina para las aplicaciones o los nodos que no son esenciales, las aplicaciones esenciales, como los núcleos de reactores, requieren una transmisión sin pérdida de datos.
• Rendimiento: el tipo y tamaño de las transmisiones de datos puede tener un gran impacto en la selección del protocolo. Los datos binarios simples que comunican un estado de activado/desactivado pueden utilizar protocolos de bajo costo y bajo rendimiento. Sin embargo, los datos de imágenes de cámaras requieren protocolos que permitan volúmenes de datos mucho mayores.
• Tiempo real/determinista: algunas aplicaciones industriales no pueden tolerar ningún retraso en las comunicaciones. Los protocolos que no funcionan en tiempo real y no pueden garantizar que los paquetes de datos se entreguen de forma inmediata simplemente no son adecuados para cubrir estas demandas. Esta consideración se menciona frecuentemente para no utilizar protocolos típicos de computadora, como TCP/IP, en en configuraciones industriales.
• Rango, carga y arquitectura de red: las distancias que los datos deben recorrer en la red, el número de nodos de la red y la arquitectura misma de la red pueden marcar una gran diferencia en la selección del protocolo. La congestión de la red, el rendimiento y la pérdida de datos pueden convertirse en elementos prominentes en ciertas arquitecturas de red. La selección de un protocolo no adecuado puede marcar la diferencia entre una planta eficiente y una planta propensa a problemas.
• Seguridad: las redes industriales necesitan protección contra amenazas no intencionales y maliciosas. A diferencia de los sitios web y otras salidas de IT, el impacto de las violaciones de seguridad no solo se puede medir en daños financieros y daños a la reputación. La seguridad humana y la seguridad nacional se pueden ver amenazadas cuando las redes sin protecciones adecuadas, como cifrado, sufren violaciones.
• Escalabilidad y extensibilidad: un factor importante también es el grado de escalabilidad y extensibilidad que se necesita. Cuando es necesario agregar nuevos nodos frecuentemente o cuando las configuraciones de la red necesitan cambios, algunas implementaciones pueden ser muy costosas. Además, algunas redes, como ZigBee, se pueden diseñar para organizarse y repararse a sí mismas cuando ocurren errores, lo que convierte a la adición o la eliminación de nuevos nodos en un proceso rápido y barato.
Todos los factores anteriores son importantes, independientemente de la capa de la red, aunque los protocolos para propósitos generales son más adecuados en las capas superiores, que tienen menor latencia y menores requerimientos de tiempo real.
Panorama de protocolos industriales
Las demandas estrictas de las redes industriales históricamente han impulsado la creación de una gran variedad de protocolos patentados y específicos para las aplicaciones. Las redes alámbricas e inalámbricas tienen sus propios conjuntos de protocolos. A pesar de la gran cantidad de protocolos disponibles, la mayoría de los protocolos alámbricos siguen dos estándares: Fieldbus o Ethernet industrial. Recientemente, la conectividad inalámbrica ha demostrado su potencial para reducir los costos de las redes, y algunos protocolos, como Wi-Fi, celular, Bluetooth y ZigBee, se están utilizando en diferentes medidas. Además, IO-Link, un protocolo en serie de punto a punto, está adquiriendo popularidad
en aplicaciones inteligentes de tipo de sensor.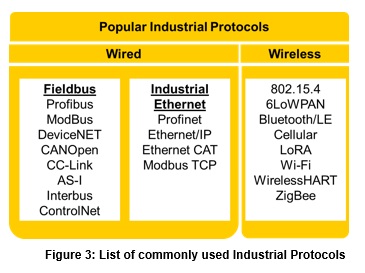
Fieldbus
Fieldbus es una familia de protocolos de red de computadoras industriales utilizados para el control distribuido en tiempo real, estandarizados como IEC 61158. Los protocolos de Fieldbus eliminaron la restricción anterior en la que solamente dos dispositivos se podían comunicar entre sí en las conexiones en serie (como RS 232). Al proporcionar solo un punto de comunicación en el nivel del controlador, cientos de nodos análogos y digitales se pueden comunicar simultáneamente utilizando los protocolos de Fieldbus. La topologías de red de tipo cadena, estrella, anillo, rama y árbol son compatibles. El mayor beneficio proporcionado por Fieldbus ha sido la gran reducción del cableado en las plantas. La siguiente tabla muestra un resumen de los diferentes protocolos de la familia y sus características. También se presentan las ventajas, las desventajas y la idoneidad de cada aplicación. Las características destacadas de confiabilidad y simplicidad han convertido a Fieldbus en el protocolo más utilizado en las redes industriales.
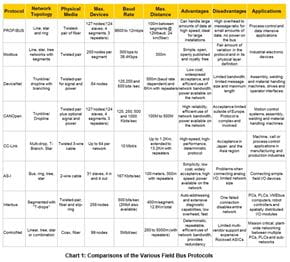
Ver Productos relacionados
Ver Productos relacionados
Ethernet Industrial:
Protocolos inalámbricos:
Las soluciones inalámbricas han generado nuevas oportunidades para ahorrar en los costos operativos de las redes y facilitar la instalación de las mismas. Aunque aún se encuentran en sus primeras fases de adopción, estos protocolos se consideran cada vez más como el futuro. Las principales ventajas son la eliminación del cableado y la capacidad de impulsar más puntos de control y monitoreo. Actualmente, los sensores y dispositivos de medición son los principales usuarios de protocolos inalámbricos. Las tecnologías inalámbricas más comunes para la automatización industrial incluyen los protocolos basados en Wi-Fi 802.11.x, Bluetooth, celular, radio ISM patentado sin licencia y 802.15.4, como WirelessHART, ISA100.11a, WIA-PA y ZigBee. La adopción de Wi-Fi suele acompañar a las implementaciones de Ethernet industrial y normalmente coexiste como un segundo soporte para las comunicaciones. Bluetooth se utiliza como un reemplazo para el cable de punto a punto, por ejemplo, entre una solución HMI y un dispositivo de campo. La conectividad celular normalmente se utiliza para redireccionar la comunicación entre plantas, conectando dispositivos remotos en aplicaciones SCADA de largo alcance y para el acceso de terceros a la maquinaria y los robots. La siguiente tabla muestra un resumen de los diferentes protocolos de la familia y sus características. También se presentan las ventajas, las desventajas y la idoneidad de cada aplicación. Con todas las nuevas posibilidades generadas por el análisis de datos y el Internet de las Cosas, los protocolos inalámbricos seguirán creciendo en el entorno industrial.
Desarrollos de mercado
Las soluciones de protocolos basados en Fieldbus que han existido durante varias décadas representan en la mayoría de los protocolos que actualmente están en uso. Según los analistas, entre el 55 y el 65 % de toda la conectividad industrial está soportada por tecnologías de Fieldbus y la tasa anual es de alrededor de un 7 %. La conectividad de Ethernet industrial ha alcanzado una popularidad global y cada vez se adopta con mayor frecuencia. Se espera que los nodos de Ethernet superen el ritmo de crecimiento de la conectividad tradicional. Sin embargo, el índice de adopción ha sido más lento de lo esperado, lo que se debe en gran medida a la seguridad, la resistencia y la tradición que ofrece Fieldbus. En general, las partes interesadas industriales muestran dudas para impulsar un cambio rápido en sus entornos, pues cualquier error puede ser catastrófico. La penetración de Ethernet ronda un 30 o 40 % en la mayoría de los pronósticos, con una tasa de crecimiento en el rango del 20 %. La base de dispositivos inalámbricos instalados en aplicaciones industriales es del 4 %, y se pronostica un crecimiento a una tasa anual compuesta del 30 %. La mayoría de los proveedores principales de dispositivos inalámbricos del Internet de las Cosas en automatización industrial ofrecen una gran variedad de soluciones con diferentes tecnologías inalámbricas para soportar muchas aplicaciones diferentes.
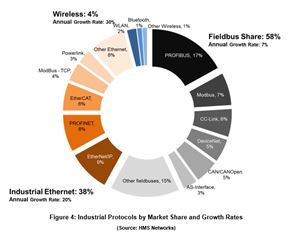
En vista de la proliferación de los dispositivos más inteligentes de bajo costo y el aumento de valor de la convergencia digital proporcionada por los protocolos modernos de Ethernet, se espera que las soluciones de Ethernet e inalámbricas tengan una mayor adopción. El Internet de las Cosas, la detección penetrante y el crecimiento de datos representan los mayores impulsores de cambio en el sector. El potencial para monitorear cada control individual y cada punto de monitoreo, así como la capacidad de reunir grandes cantidades de datos para alimentar los esquemas avanzados de mantenimiento preventivo, son de gran interés para los profesionales de la industria. El valor de integración de los sistemas empresariales y los sistemas operativos tiene una particular importancia. La mayoría de las empresas están adoptando modelos operativos de nube (pública y privada) para disminuir el costo total de la propiedad de su infraestructura de TI. Es probable que el paradigma de nube también se adopte en los sistemas de control de la siguiente generación. Las limitaciones actuales del rendimiento de datos y la seguridad ya no serán suficientes conforme las nuevas estrategias predicadas en la recolección de grandes cantidades de datos se vuelvan más predominantes.
Aunque es difícil predecir la desaparición de una tecnología frente a otra, la enorme base de dispositivos instalados de Fieldbus y su comunidad de expertos indican un futuro en el que las tecnologías de Ethernet, Fieldbus e inalámbricas coexistirán durante muchos años.